Photo Sensor
Introduction to different types of object detection Photo Sensor There are many types of object detection photo sensors available on the market. Some of them, such as photoelectric, laser and ultrasonic sensors. Photoelectric sensors use reflected or detected light waves to detect object presence or distance in a wide range of industrial applications. They typically contain all required optics and electronics in a single unit, requiring only power to provide an output based on their specifications and object detection criteria. PEN series of HANYOUNG photoelectric sensors has been shown in figure.1
Table Of Contents Of This Article
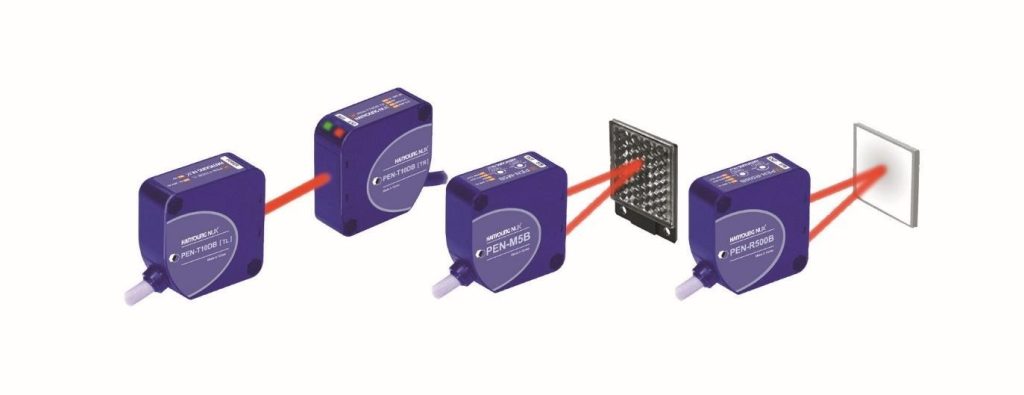
Fig 1: PEN series
Some important features of this model include: Model: PEN-T10A, PEN-M5A, PEN-R700A PEN
T10A:
- Through-beam(sensing type)
- 10m(sensing distance)
- Opaque object over Ø 20 mm(detecting object)
- 24-240Vac/dc(power voltage)
- Light-on /Dark-on(operation mode)
- Relay output(control output)
PEN-M5A:
- Retro- reflective(sensing type)
- 1-5m(sensing distance)
- Opaque object over Ø 60 mm(detecting object)
- 24-240Vac/dc(power voltage)
- Light-on /Dark-on(operation mode)
- Relay output(control output)
PEN-R700A:
- Diffuse- reflective(sensing type)
- 700mm(sensing distance)
- White non-glossy paper 200*200mm(detecting object)
- 24-240Vac/dc(power voltage)
- Light-on /Dark-on(operation mode)
- Relay output(control output)
Photoelectric sensors can detect a wide variety of materials and have extended sensing ranges. Other object detection sensors are available for specialized applications. Some specialty sensors available that work similarly to a photoelectric sensor are laser sensors, fiber optic sensors, fork sensors, and area sensors. Although not seen as often as other types of sensors in the automation industry, they can be vital to an application with unique needs
Photoelectric sensors- rectangular-OS10 (ELCO)
Mini-rectangular photoelectric sensors OS10 series, with high performance and 25.4mm standard mounting hole distance, are available as BGS (background suppression) mode, Diffused mode, retro-reflective mode, and opposed mode. With optional red beam or laser beam source. They are suitable for printing and packaging, pharmaceutical, electronic, small equipment and other application fields. OS10 series of ELCO photoelectric sensors has been shown in figure.2
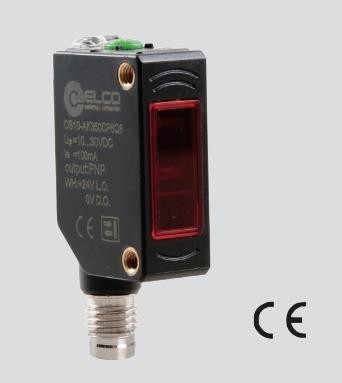
Fig 2: OS10 series
Some important features of this model include:
- BGS function greatly improves the detection effect
- Optional red beam or laser beam
- Adjustable sensing range
- Protection class IP67
- Optional M8 connector , 2m pre-wired cable
BGS-Background Suppression Function
Standard diffused mode photoelectric sensors detect the objects according to the value of the received light, which is dependent on object color, material, transparency and other factors. Therefore, even using the same type of diffused photoelectric sensor to detect different objects, the sensing ranges vary dramatically.
By using dual diode receiver, the BGS mode photoelectric sensors detect the object according to the different position that reflected light falls on the receiver.
As shown in figure.3, when the sensor relatively close to the object, the reflected light falls on receiver Red position, at this time, the output is turned ON. The sensing rage of the photoelectric sensors whit BGS is basically the same for various objects.
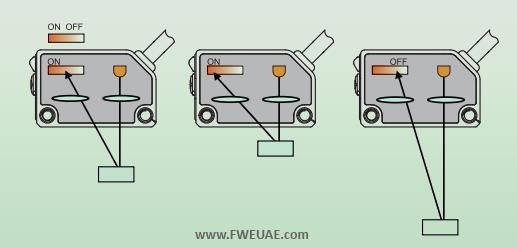
Fig 3: OS10 series (BGS)
Sensors have many different options when it comes to the output signal. The output can be an electromechanical relay contact or it can be solid state. If it is a solid state output, then the logic can be NPN or PNP. Either type of output can be Normally Open (NO) or Normally Closed (NC).
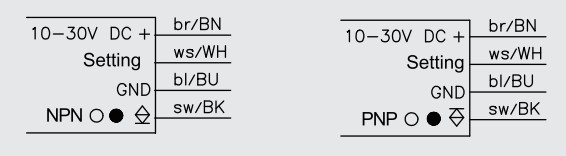
An electromechanical relay output uses a physical set of contacts that open or close to switch a signal. This works very similarly to a light switch in your house. It is either fully open or fully closed. The advantages of a relay contact output are that the signal is either fully ON or fully OFF and this type of output circuit usually can handle much higher current draw through it. A drawback of a relay contact is that since it is mechanical, it will eventually wear out after extended use and either weld closed or be stuck open.
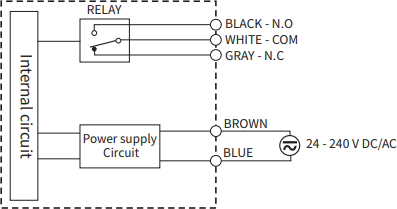
Solid state devices use no moving or mechanical parts and essentially have an infinite lifespan if they are not overloaded. They are smaller than relay contacts and make no noise when switching the output signal. Some drawbacks to solid state devices are that they usually do not handle as much current as a relay contact, and they are never truly completely OFF or completely ON so they will have some leakage current in their OFF or open state.
For DC solid state outputs, an important consideration to take into account is whether the logic of the sensor output needs to be NPN or PNP (other terms to describe the same logic is sinking versus sourcing).
To properly wire your control device, you need to first know whether the sensor you are using is switching the positive or negative connection. For AC (alternating current) sensors, this is not an issue since AC power
alternates its polarity 120 times per second with 60-HZ current and AC sensors are designed for that. On the other hand, DC (direct current) sensors only allow current flow in one direction and therefore have a constant polarity that must be considered.
With DC sensors, NPN and PNP may be terms you hear quite often. These terms define the Collector, Base and Emitter polarities of the transistor itself. In these transistors, the ON and OFF switching is accomplished between the Collector and Emitter legs, and the Base (controlled by the sensor) will determine when that happens. How the transistor closes the control circuit will determine if it’s a sinking or sourcing output.
Normally open versus normally closed are terms used to describe whether the output is ON or OFF based on the sensor’s normal state. This is a throwback term from when the only output option was a relay contact and solid state switches didn’t exist. However, today we use the same terms to describe solid-state or relay outputs.
If the output is described as being closed, then the output is ON, just like when a relay contact or light switch is closed the output will be ON.
When an output is described as being open then the output is OFF, exactly the opposite of being closed.
The “normal” state of a sensor means that the sensor is not detecting an object.
So for example, if any type of sensor has a normally open output and it does not detect an object, then the output will be OFF and will turn ON when it detects an object.
Likewise, if a sensor has a normally closed output, the output will be ON when it does NOT detect an object and the output will then turn OFF when an object is detected.